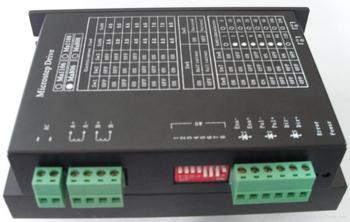
This new technology not only eliminates the need for a mechanical motor rotor sensor, reduces system cost, but also enables the latest software encoder (sensorless observer) algorithm embedded in read-only memory (ROM) on TI's 32-bit C2000® PiCColo microcontrollers. FAST (flux, angle, speed and torque) to improve work. InstaSPIN-FOC belongs to the previously launched InstaSPIN-BLDC technology, and will introduce various InstaSPIN solutions in the future to make motor control development easier and more efficient.
Improving motor system reliability and efficiency Although sensorless FOC motor technology offers many system advantages, many industries have had to delay the adoption and promotion of these technologies due to lack of knowledge of motor control systems. InstaSPIN-FOC not only helps designers to simplify development, reduces system cost and complexity, even for designers with limited motor control experience, but also enables excellent solutions to improve all variable speed and load motor applications. Motor efficiency, performance and reliability. In traditional FOC motor designs, the use of rotor sensors increases costs (requires sensors, power supply, special wiring and connectors, installation, and maintenance) and may also degrade reliability (dear performance degradation, electrical noise, and vulnerability Temperature and humidity effects, which have an adverse effect on the system. In addition, the use of sensors in many applications such as hermetic compressors or large traction equipment is completely impractical.
Features and Benefits of InstaSPIN-FOC Technology: Design time is reduced by several months: Since identification and control adjustments are almost fully automated, designers can differentiate their product functions based on full motor torque; proximity encoder performance : Reliable, robust estimation of flux, angle, speed and torque under various conditions of use using the embedded on-chip FAST observer algorithm. With accurate sensorless "estimators", in most cases no physical encoder is required; all three-phase motors are supported: the same solution supports synchronization (BLDC, SPM and IPM) and asynchronous (ACI); identification and regulation: off-line motors Commissioning identifies the required motor electrical parameters, adjusts the FAST algorithm, and initializes the current controller to ensure stable operation. In addition, an optional on-line resistive re-evaluation mode is provided to track changes in the performance of high-stability observers under the harshest conditions; start-up challenges can be avoided: support for built-in startup modes and observer angle locking for less than one electrical cycle, can be Avoid start-up challenges with other sensorless technologies; Low-speed performance: Angle integrity can be maintained at sub-1Hz (typical) full-torque stability, supporting zero-speed reversal and smooth stall recovery in stall conditions; single function calls can be implemented Increased flexibility: FOC torque controllers (supporting up to 2 motors from the same ROM) or fully customized FAST control systems can be used as motor sensors; support for the most efficient motor finalization: built-in magnetic field control can be provided manually or Automatic field weakening (higher speed) or manual field strength (higher torque) applications; large energy savings possible: for induction motors with PowerWarp® mode, avoiding wasted energy when torque is not needed immediately; easy to develop, Quick evaluation: With MotorWareTM using the latest motor control libraries (modules, drives, system examples and documentation), Like, C language code based on the latest technology API. Lab meter testing can be performed with TI's latest free GUI Composer tool.
Custom Medical Cable Assemblies,Custom Medical Wire,Custom ECG Cable,Custom Sensor Cable
Dong guan Sum Wai Electronic Co,. Ltd. , https://www.sw-cables.com